Compressed Air Audit & Operational Improvements
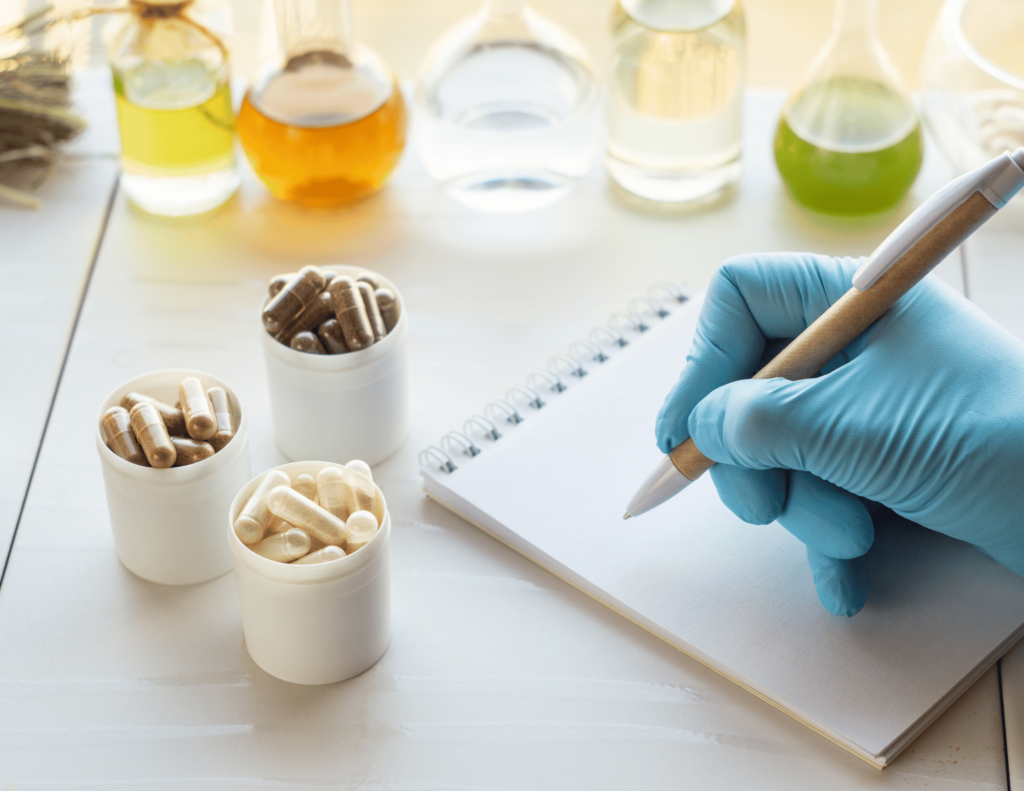
Facility Type
Dietary Supplement Manufacturing Facility
Facility Size
50,000 SF
Initial Challenge
- The facility’s 2-75 HP compressors were running almost 24/7/365.
- Production operated only 2 shifts per day, 5 days a week.
- Annual energy cost: $88,186.
- Numerous leaks in the compressed air distribution system.
- Equipment operating when not needed
Step 1:
Compressed Air Audit
Projected Savings:
Base Case:
- 150 HP, 111.9 kW, 8,760 Hours/Year, 979,850 kWh/Year, $88,186.48.
Reduced Operation:
- 150 HP, 111.9 kW, 5,224 Hours/Year, 584,331 kWh/Year, $52,589.75.
Assumed Savings:
- 3,536 Hours/Year, 395,519 kWh/Year, $35,596.74.
Actions Taken:
- Installed data loggers to identify leaks.
- Fixed leaks in the compressed air distribution system.
- Corrected equipment settings.
- Turned off compressors when production wasn’t running.
Step 2:
Operational Improvements
Facility Walk-Through Observation:
- Production operators used air nozzles to clean encapsulation equipment.
- Significant amounts of raw material ended up on the floor, not in the capsules.
Procedural Changes:
- Removed air nozzles from five encapsulation production rooms.
- Trained operators to sweep extra powder into a sanitary container to be reused in the raw material feed.
Our Impact in Figures
Months
On an energy audit and repairs that cost $10,000.
/Year
Reduction in raw material scraps.
/Year
Reduction in maintenance costs.
Increase in production equipment availability.
/Year
Achieved annual energy savings.
Other Recent Projects
Facility Type: Warehouse, Distribution, and Production Batch Kitting Facility
Facility Type: Encapsulation and Bulk Powder Manufacturing Facility
Compressed Air Audit & Operational Improvements
Facility Type
Dietary Supplement Manufacturing Facility
Facility Size
50,000 SF
Initial Challenge
- The facility’s 2-75 HP compressors were running almost 24/7/365.
- Production operated only 2 shifts per day, 5 days a week.
- Annual energy cost: $88,186.
- Numerous leaks in the compressed air distribution system.
- Equipment operating when not needed
Step 1
Compressed Air Audit
Projected Savings:
Base Case:
- 150 HP, 111.9 kW, 8,760 Hours/Year, 979,850 kWh/Year, $88,186.48.
Reduced Operation:
- 150 HP, 111.9 kW, 5,224 Hours/Year, 584,331 kWh/Year, $52,589.75.
Assumed Savings:
- 3,536 Hours/Year, 395,519 kWh/Year, $35,596.74.
Actions Taken:
- Installed data loggers to identify leaks.
- Fixed leaks in the compressed air distribution system.
- Corrected equipment settings.
- Turned off compressors when production wasn’t running.
Step 2:
Operational Improvements
Facility Walk-Through Observation:
- Production operators used air nozzles to clean encapsulation equipment.
- Significant amounts of raw material ended up on the floor, not in the capsules.
Procedural Changes:
- Removed air nozzles from five encapsulation production rooms.
- Trained operators to sweep extra powder into a sanitary container to be reused in the raw material feed.
Our Impact in Figures
On an energy audit and repairs that cost $10,000.
Reduction in raw material scraps.
Reduction in maintenance costs.
Increase in production equipment availability.
Achieved annual energy savings.
Other Recent Projects
Facility Type: Encapsulation and Bulk Powder Manufacturing Facility
Facility Type: Warehouse, Distribution, and Production Batch Kitting Facility